Abstract : Lyocell fiber has excellent physical and mechanical properties, and its versatility in the feel and appearance of knitted fabrics makes its development and application prospects very broad. Amicor is a kind of fiber with good antibacterial properties. In this paper, 19.7tex Lyocell/Amicor fiber antibacterial knitting yarn is processed by rotor spinning technology. The relationship between the main process parameters of rotor spinning and the quality of yarn forming is studied through the comparison of various schemes. Reasonable selection of process parameters to improve the yarn quality of rotor knitting yarn provides a reference.
0 , introduction
One of the main products of Lyocell fiber is knitted underwear, casual wear, etc. Its products have the body touch and drape similar to natural fiber, especially the light knit fabric, which is the most ideal material for women's underwear. It absorbs sweat, keeps warm and cool, and combines the comfort of cotton, the drape of glue, the strength of polyester and the feel of silk.
Amicor fiber is a new type of antibacterial fiber developed by ACORDIS in the UK. Often used to blend with cotton, polyester, Tencel, wool and other fibers. When a small amount of Amicor component is mixed in the blended yarn, it not only has good antibacterial properties, but also hardly changes the hand feeling and style of the original fabric and the textile processing property of the main component fiber [1] .
Amicor fiber fabric can inhibit the growth of bacteria, has long-term antibacterial effect, is resistant to washing, and is washed 200 times at any temperature within 100 ° C. Its antibacterial effect is unchanged, and its excellent antibacterial activity in the presence of blood, sweat and urine. The effect is not affected [2] .
The rotor yarn is evenly dried and has few details, and the head rate is reduced during the knitting process, and the production efficiency is high. Generally, the yarn breakage of the rotor yarn can be reduced by 60% compared with the use of the ring yarn, and the speed of the knitting machine can be increased by 10% to 15%. Lyocell fiber yarn is easy to produce hairiness. The rotor yarn is formed by disposable bobbin. The yarn has less hairiness and the appearance of the knitted fabric is clear and full, which can produce high quality printed fabric. Rotor knitting yarn also has the advantages of less yarn defect, good elasticity, anti-pilling and wear resistance. In order to develop and adapt to the needs of the current market, the research and development of 19.7tex Lyocell/Amicor health care knitting products was carried out.
1 , processing conditions
Using BD200SN rotor spinning machine to process 19.7tex blended yarn, Lyocell/Amicor mixing ratio: 70/30, φ43 rotating cup, OK37 sawtooth separating roller, spiral ceramic false twisting disc, sliver weight 14.2g/5m, The temperature is 25 ° C and the relative humidity is 75%.
2 , spinning scheme design, processing and performance testing
A quadratic general rotation combination design was used to arrange the test protocol. Compared with the traditional orthogonal test, the method has fewer trials and simple calculations; eliminates error interference, predicts and estimates the results of non-test points through the established quadratic regression equation, and the predicted values ​​can better reflect the objective conditions. . Rotate the combined design factor coding table, see Table 1.
Table 1 Factor coding table (r=1.682)
| Rotor speed (r/min) | Opening roller speed (r/min) | æ» coefficient |
+ p | 55000 | 8000 | 330 |
+1 | 53986 | 7919 | 320 |
0 | 52500 | 7800 | 305 |
-1 | 51014 | 7681 | 290 |
- p | 50000 | 7600 | 280 |
According to the three-factor quadratic general rotation combination design table, 20 sets of test schemes were obtained. The implementation sequence of the test plan implements a random principle with the aim of eliminating systematic errors. After the spinning and yarn performance test, the abnormal value of the yarn performance data was tested by the extreme value deviation method in the mathematical statistics method, and the abnormal data was eliminated. The trial spinning scheme and yarn performance data are shown in Table 2 and Table 3, respectively.
Table 2 Trial spinning scheme
experiment Serial number | Rotor speed (r/min) | Opening roller speed (r/min) | æ» coefficient |
1 | 53986 | 7919 | 320 |
2 | 53986 | 7919 | 290 |
3 | 53986 | 7681 | 320 |
4 | 53986 | 7681 | 290 |
5 | 51014 | 7919 | 320 |
6 | 51014 | 7919 | 290 |
7 | 51014 | 7681 | 320 |
8 | 51014 | 7681 | 290 |
9 | 55000 | 7800 | 305 |
10 | 50000 | 7800 | 305 |
11 | 52500 | 8000 | 305 |
12 | 52500 | 7600 | 305 |
13 | 52500 | 7800 | 330 |
14 | 52500 | 7800 | 280 |
15 | 52500 | 7800 | 305 |
16 | 52500 | 7800 | 305 |
17 | 52500 | 7800 | 305 |
18 | 52500 | 7800 | 305 |
19 | 52500 | 7800 | 305 |
20 | 52500 | 7800 | 305 |
Table 3 Quality indicators of yarns in each scheme
experiment Serial number | Dry (CV%) | Breaking strength (cN/T) | Elongation at break (%) | Hairiness index (/m) | Details / km (-50%) | Thick section/km (+50%) | Neps/km (+200%) |
1 | 15.89 | 15.41 | 5.66 | 4.48 | 25 | 83 | 127 |
2 | 15.92 | 14.62 | 5.12 | 6.54 | 40 | 80 | 120 |
3 | 17.18 | 15.52 | 5.58 | 4.70 | 35 | 96 | 130 |
4 | 17.47 | 14.74 | 5.35 | 6.32 | 44 | 97 | 133 |
5 | 16.27 | 15.37 | 6.08 | 4.52 | 15 | 56 | 86 |
6 | 16.33 | 14.58 | 5.28 | 6.88 | 25 | 57 | 85 |
7 | 15.63 | 15.53 | 6.37 | 7.72 | 25 | 70 | 96 |
8 | 16.54 | 14.64 | 5.54 | 8.90 | twenty four | 71 | 97 |
9 | 15.18 | 14.61 | 4.84 | 3.64 | 51 | 103 | 170 |
10 | 15.69 | 14.62 | 6.51 | 6.30 | 11 | 50 | 92 |
11 | 17.63 | 13.05 | 6.16 | 7.98 | 26 | 63 | 95 |
12 | 17.87 | 13.12 | 5.79 | 5.48 | 32 | 90 | 145 |
13 | 15.18 | 16.98 | 6.95 | 4.10 | 34 | 76 | 111 |
14 | 15.39 | 15.43 | 5.28 | 10.0 | 42 | 75 | 110 |
15 | 15.46 | 16.21 | 5.36 | 4.63 | 32 | 81 | 115 |
16 | 15.23 | 16.18 | 5.55 | 5.24 | 36 | 73 | 112 |
17 | 15.19 | 16.35 | 5.48 | 5.44 | 38 | 75 | 115 |
18 | 15.27 | 16.32 | 5.86 | 5.18 | 31 | 77 | 105 |
19 | 15.29 | 16.21 | 5.45 | 4.42 | 37 | 79 | 107 |
20 | 15.47 | 15.98 | 5.65 | 5.64 | 30 | 78 | 102 |
3 , establish a mathematical model
The general formula of the three-factor quadratic regression equation model is as follows: 
Use MATLAB7.0 software to write a program for solving regression equations. After computer calculation, the regression coefficients of the regression equations of each index are obtained. Through the significance test of the regression equation, the regression equations of strip, fracture strength and thick section are significant at α=0.01, and the regression equations of other indicators are significant at α=0.05. The initial regression equation is shown in Table 4. .
Table 4 Initial regression equations for each indicator
Indicator | Equation |
Dry | Y=15.308+0.061x 1 -0.206x 2 -0.12x 3 -0.409x 1 x 2 +0.081x 1 x 3 +0.139x 2 x 3 +0.085x 1 2 +0.903x 2 2 +0.031x 3 2 |
Breaking strength | Y=16.188+0.011x 1 -0.042x 2 +0.429x 3 -0.001x 1 x 2 -0.014x 1 x 3 -0.011x 2 x 3 -0.454x 1 2 -0.995x 2 2 +0.109x 3 2 |
Elongation at break | Y=5.567-0.32x 1 -0.006x 2 +0.381x 3 +0.05x 1 x 2 -0.108x 1 x 3 +0.035x 2 x 3 -0.026x 1 2 +0.08x 2 2 +0.13x 3 2 |
Hairiness index | Y=5.092-0.765x 1 -0.074x 2 -1.255x 3 +0.653x 1 x 2 -0.018x 1 x 3 -0.203x 2 x 3 -0.056x 1 2 +0.567x 2 2 +0.68x 3 2 |
detail | Y=34.145+8.221x 1 -3.155x 2 -2.669x 3 -1.875x 1 x 2 -0.625x 1 x 3 -0.875x 2 x 3 -2.051x 1 2 -2.758x 2 2 +0.424x 3 2 |
Thick section | Y=77.144+13.995x 1 -7.572x 2 +0.123x 3 -0.25x 1 x 2 +0.50x 1 x 3 +0.50x 2 x 3 -0.196x 1 2 -0.196x 2 2 -0.55x 3 2 |
Neps | Y=109.69+20.295x 1 -8.94x 2 +0.416x 3 +0.75x 1 x 2 +0.50x 1 x 3 +1.50x 2 x 3 +5.158x 1 2 +1.268x 2 2 -2.091x 3 2 |
Then pass the regression coefficient significance test. At the α=0.05 level, the regression coefficients that are not significant in the regression equations of each index are eliminated, and the final regression equations of each index are obtained, as shown in Table 5.
Table 5 final regression equations for each indicator
Indicator | Equation |
Dry | Y=15.395-0.206x 2 -0.409x 1 x 2 +0.893x 2 2 |
Breaking strength | Y=16.277-0.464x 1 2 -1.006x 2 2 +0.429x 3 |
Elongation at break | Y=5.693-0.32x 1 +0.381x 3 |
Hairiness index | Y=5.4728-0.765x 1 -1.255x 3 +0.634x 3 2 |
detail | Y=31.150+8.221x 1 |
Thick section | Y=76.501+13.995x 1 -7.572x 2 |
Neps | Y=112.651+20.295x 1 -8.94x 2 |
4 , analysis of test results According to the regression equation between the process parameters and the yarn forming index, the MATLAB7.0 software is used to draw the three-dimensional surface and the contour curve, and the process parameters such as the opening speed, the rotor speed and the twist coefficient are analyzed for Lyocell/Amicor. The influence of the quality of the yarn into the yarn.
4.1 dry
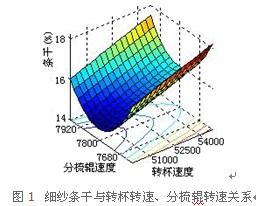
It can be seen from Fig. 1 that when the speed of the opening roller is lower than 7800r/min, the drying of the yarn becomes gradually improved with the increase of the rotation speed of the opening roller. After exceeding 7800r/min, the strip is rapidly deteriorated. The increase of the rotational speed of the opening roller makes the carding effect strong, the weight percentage of the single fiber is significantly improved, and the dryness of the yarn is improved, but the elongation of the Lyocell fiber is small, the rebound resilience is poor, and the fiber is easily damaged, with the opening roller The rotation speed continues to increase, the fiber damage is severe, and the level of the strip is gradually deteriorated.
As the speed of the rotor increases, the level of the strip is gradually deteriorated. This is because the feeding speed of the sliver is increased and the fiber combing effect is weakened. At the same time, the inherent fibrillation characteristics of the Lyocell fiber are easily produced during the processing. A large number of thick knots and neps make the stem level drop.
4.2 breaking strength
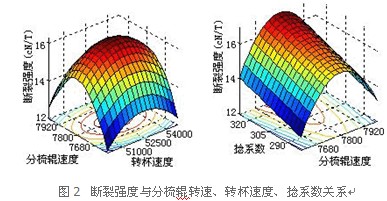
When the rotor speed is increased, the vacuum in the rotor cup is increased, so that the fiber has a good straightness orientation and an increased yarn breaking strength during the process from the conveying pipe to the rotor cup condensing groove. However, when the rotor speed exceeds a certain critical value (53000 r/min), the average number of teeth of the carding roller of each fiber is reduced due to the faster feeding speed of the sliver, the combing effect is weakened, and the number of bundle fibers is increased. The number of fibers flowing through the cotton pipe per unit time increases, which makes the fiber separation degree and orientation degree worse, and the yarn breaking strength begins to gradually decrease.
As the rotational speed of the opening roller increases, the carding effect is strong, the weight percentage of the single fiber is remarkably improved, and the strength of the single yarn is gradually increased. However, after the opening speed of the opening roller exceeds 7800r/min, the fiber continues to increase, the fiber is continuously damaged, and the rate of the short pile is increased, so that the breaking strength is gradually decreased.
As the enthalpy coefficient increases, the centripetal pressure of the fiber on the yarn axis increases, the frictional resistance between the fibers increases, and the rupture strength of the yarn gradually increases.
Therefore, for the breaking strength of the yarn, when the opening speed of the opening roller is 7800 r/min, the rotating cup is 53000 r/min, and the æ» coefficient is 330, the breaking strength of the yarn reaches a peak.
4.3 elongation at break
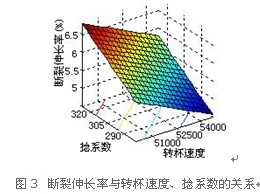
Figure 3 shows that the elongation at break increases linearly with increasing enthalpy coefficient. This is because the increase in the enthalpy coefficient increases the fiber inclination angle, and the inclination angle at the time of stretching tends to decrease, thereby increasing the elongation at break of the yarn.
The higher the rotor speed, the greater the tension of the sliver, which also reduces the elongation at break of the yarn.
4.4 hairiness
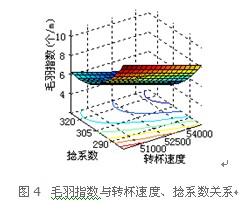
Figure 4 shows that the number of yarn hairiness decreases as the twist factor and rotor speed increase. Increasing the enthalpy coefficient can increase fiber penetration into the yarn body and reduce the chance of exposure, so the number of hairiness decreases with increasing enthalpy coefficient. The yarn tension is greatly increased with the increase of the rotor speed, so that the yarn is tight and the wrapped fibers are tightly packed, and the number of hairiness is reduced.
Lyocell fiber has high modulus, many yarn hairiness, and Lyocell fiber has fibrillation characteristics. If the æ» coefficient is too small, the fabric will easily rub the ball and produce fur in the post-processing and wearing process [3] . Therefore, selecting a slightly larger enthalpy coefficient not only reduces the hairiness of the Lyocell yarn, but also improves the yarn strength, and is advantageous for suppressing the fibrillation tendency of the Lyocell fiber fabric.
4.5 details, thick sections, nep
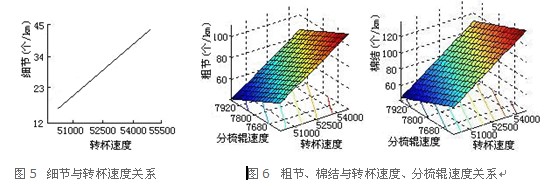
Figure 5 and Figure 6 show that the details, the number of knots, and the number of neps increase with the increase of the rotor speed, and the number of knots and neps decreases with the increase of the speed of the opening roller. Increasing the speed of the rotor, the number of fibers fed per unit time also increases, the carding effect of the fibers is weakened, the fiber separation degree is deteriorated, and the details, the number of knots, and the number of neps are correspondingly increased. At the same time, the cotton bundle is prone to tilting movement in the cotton pipe, and friction with the pipe wall increases the number of neps. Therefore, while increasing the speed of the rotor, the speed of the opening roller can be appropriately increased, so that the number of thick knots and neps can be kept relatively small.
5 , other technical essentials
The weight of the cooked strip is lightly controlled, which can reduce the load of the opening roller, facilitate the carding and transfer of the fiber, and improve the drying of the yarn.
Lyocell fiber yarn is easy to produce hairiness. The yarn speed of the rotor should be properly controlled. Low-tension spinning should be used to avoid the friction of the yarn body during winding.
The use of a spiral ceramic false twist plate allows the Lyocell rotor yarn to have fewer broken ends, less hairiness and a higher level of dryness.
6 , the conclusion
(1) For the processing of Lyocell/Amicor blended rotor-knit yarn, the process parameters of rotor spinning should be reasonably selected to produce high-quality yarn.
(2) Through the above analysis, the No. 13 program is a reasonable process plan. Namely: the opening speed of the opening roller is 7800r/min, the rotor speed is 52500r/min, and the æ» coefficient is 330.
(3) The ceramic false twisting disc is used to properly control the yarn feeding speed of the rotor, and the low tension spinning is adopted.
(4) The knitted fabric developed by the blended yarn processed by the No. 13 scheme has good taking performance, has a body touch and drape which resembles natural fiber, is smooth and flowing, absorbs sweat, is warm and cool, and has high strength and wear resistance. Excellent in sex and elasticity, with good antibacterial effect, it is an ideal health care underwear fabric.
PVC Shower Hose
Pvc Shower Hose,Shower Hose Pipe,Plastic Pvc Shower Hose,Shower Hose For Hand Shower
kaiping aida sanitary ware technology co.,ltd , https://www.aidafaucets.com